Modern quarry equipment used in large mining enterprises has high-power engines that are subject to significant wear and require regular maintenance. To ensure uninterrupted operation and maximum efficiency, it is important not only to timely identify potential problems, but also to use advanced methods of diagnosis and repair. In this article, we will consider modern approaches to diagnosing and overhauling quarry equipment engines that allow to keep them in optimal condition and provide a long service life. Main methods of diagnosis and repair of quarry equipment engines Modern quarry equipment engines are mainly equipped with high-tech diagnostic systems that provide operators and technical staff with detailed information about the engine’s condition in real time. These systems monitor and record key parameters such as engine temperature, oil pressure, fuel level, vibration, and other important indicators. They allow to detect abnormal changes in engine operation that may indicate the presence of problems or potential risk of breakdown. In addition, some systems can be set up to trigger emergency signals or automatically shut down the engine in case of serious malfunction, ensuring an immediate response to critical situations. The use of such systems significantly increases the reliability and safety of quarry equipment operation, as well as reduces costs for maintenance and repairs. Vibration analysis Vibration analysis is a key method for determining the condition of moving parts of the engine, such as bearings, shafts, and pistons. This method involves monitoring and analyzing vibrations generated during engine operation. Abnormal vibrations can indicate uneven wear or faults in moving parts, which can lead to serious breakdowns. Vibration analysis enables timely detection of these problems and implementation of appropriate measures to eliminate them, helping to increase engine service life and reduce the likelihood of unexpected production downtime. Modern vibration monitoring systems can automatically analyze information and generate reports, simplifying the monitoring and support process. Infrared thermography Infrared thermography is used to detect thermal anomalies in cooling systems, exhaust systems, and other key engine components. It is based on measuring infrared radiation emitted from the surface of objects, and allows to determine temperature differences that can indicate potential problems such as inadequate coolant circulation or wear of seals. Infrared thermography enables prompt identification of these problems before they can lead to serious damage or equipment shutdown. The use of this method contributes to increased safety and reliability of quarry equipment operation and reduces the risks of unforeseen repair costs. Analysis of lubricant materials and lubrication systems Effective lubrication system is an important aspect for ensuring the long-term operation of the engine. Analysis of lubricant materials and lubrication systems includes monitoring the condition of the lubricant, assessing its wear and cleanliness. Insufficient lubrication or the use of poor-quality lubricant materials can lead to wear of moving parts, increased friction, and overheating. Systematic analysis enables timely detection of these problems and replacement of lubricant materials as needed, ensuring optimal engine performance efficiency and increasing its service life. Conclusion Modern methods of diagnosing and repairing quarry equipment engines play a vital role in ensuring reliability and efficiency of this important technology. The use of advanced technologies allows to promptly identify potential problems and timely conduct necessary repair measures, minimizing operating costs and maintaining optimal productivity levels. Regular application of these methods ensures a long service life of quarry equipment engines and reduces the risks of unforeseen stops and repair costs.
Modern Methods of Diagnosis and Repair of Quarry Equipment Engines
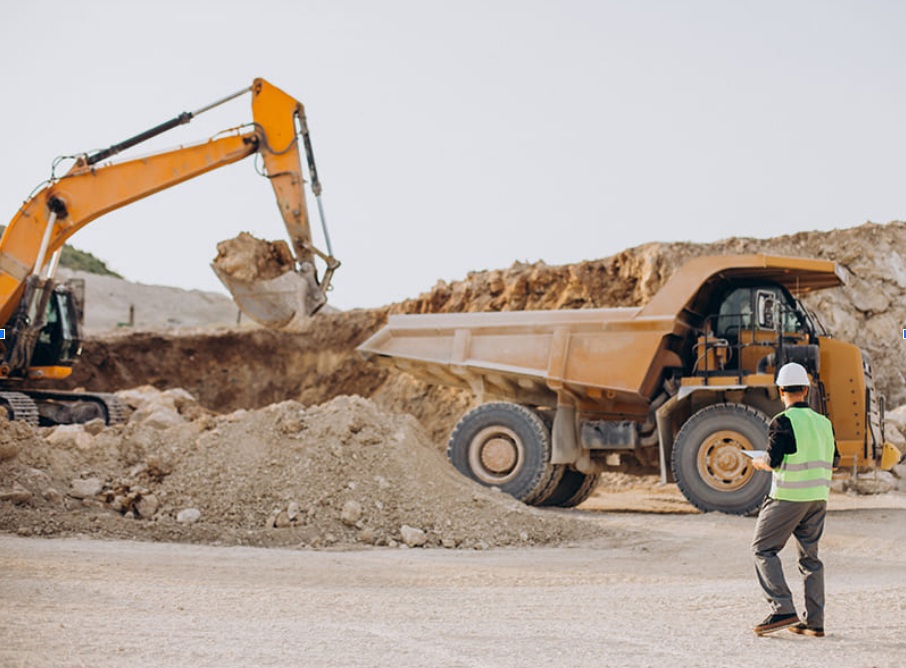